Beyond Compliance: How HR Can Help Build a Best-in-Class Safety Culture
On March 25, 1911, just about at quitting time, the young women of the Triangle Shirtwaist Factory in New York’s garment district were packing up their belongings for the day. A fire flared up in a scrap bin— believed to be caused by the careless disposal of a cigarette.
Twenty minutes later 146 people had died as a result of the inferno on the eighth floor.
Why? The doors to the factory had been locked by management to prevent theft, there was no audible alarm, there were not enough staircases, and there was only a poorly made fire escape that was so flimsy it collapsed under the weight of the people crowding onto it to escape the smoke and flames.
The calamity was recorded as one of the worst industrial accidents in U.S. history—caused mainly by the owners’ indifference to safety.
Fast forward a hundred years, and management attitudes about worker well-being have changed significantly. Triangle and similar preventable disasters at the turn of the 20th century inspired a new scrutiny of workplace and factory safety that profoundly changed working conditions in America.
See also: Promoting Safe Behavior With Safety Incentive Programs and Recognition
Yet, according to the Safety Training CenterOpens in a new tab, even today “16 workers die each day from injuries sustained at work in the U.S. […] and, more than 130 die each day from diseases resulting from exposure to workplace hazards over time.”
That’s 146 people a day, if you’re counting… same as the death toll in the Triangle Shirtwaist Fire.
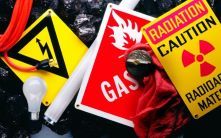
We’ve come a long way, but clearly we can still do better. Compliance with regulations is just a first step.
In fact, top companies go far beyond the letter of the law to build safety cultures that not only keep workers safer, but increase their productivity and company profitability.
OSHA has set up a program to recognize these companies, which go beyond requirements in protecting their workforce, involve their employees in all aspects of the health and safety process, and establish exemplary safety and health programs.
So, what can HR do to help build a safety culture in our organizations? The difference between a compliant program and a true culture of safety seems to lie in promoting three key areas: Inspiration, Ownership and Reinforcement.
Inspiration:
Exemplary safety organizations are able to create commitment among employees and generate passion for a culture of safety. This comes both from strong leadership at the top, which reverberates through all levels of the organization.
That’s something HR can lead. In fact, according to The Conference Board, exemplary safety organization share two qualities:
- A firm conviction that accidents and injuries are unacceptable in their operations
- A strong belief that business benefits directly from safety through reduced costs—and indirectly through improved morale and increased productivity
HR best practices for creating inspiration:
- Rally the company around core values related specifically to your safety initiative. Globoforce’s Derek Irvine has suggested structuring the safety program firmly on values such as: innovation, courage, leadership and proactive risk elimination.
- Share stories about and provide public recognition to celebrate employees who embody those safety values.
- Involve senior leadership in communication around safety, so it is clear commitment comes from the top.
Ownership:
Committed participation on all levels has been proven to be critical for a successful safety culture. HR can play a strong role in opening communication and building accountability among all stakeholders. According to OSHA, employee involvement means:
- Shared ownership of and commitment to the program
- Active support of the program
- Accountability for one’s personal safety and that of coworkers
HR best practices for creating ownership:
- Encourage employees to look beyond numbers to improve actual processes and behaviors. (A singular emphasis on safety metrics can sometimes backfire and encourage workers to conceal or minimize problems. By taking into account individual behavior and accountability you can encourage ownership and safety integrity on a personal level.)
- Encourage operations to give employees a specific role in safety programs and offer ways to participate in a meaningful way—even if that is simply by observing and acknowledging the safety related success of others.
- OSHA suggests companies engage in regular dialogue with employees. Open the lines of communication to offer stress-free reporting and to solicit constant input and suggestions for improvement.
Reinforcement:
For a safety program to be ongoing and effective, it must be reinforced and encouraged in continuous way, every day. It should also shift the emphasis from violations and fear and refocus it on positive, proactive behavioral change.
Many companies are merging the ideas of positive reinforcement and JIT operational strategies –by harnessing the power of “just-in-time” recognition, they can immediately recognize and reward safe behavior—building buy-in and trust.
HR can help most effectively in this area by installing a formal recognition program for giving positive feedback and reinforcement for safe behavior.
HR best practices for creating reinforcement:
- Refocus on the positive by designing a safety program that lets employees catch one another engaging in safer practices, and then reward that behavior.
- Put emphasis on safe processes and behaviors and minimize attention to safety metrics (such as days without an incident) which might actually impede reporting.
- Offer consistent, thoughtful safety education based on input from employees, about known issues and “near-misses”.
- Offer transparent reporting and monitor performance regularly—not simply infractions but also day-to-day activity.
Have you had success in creating a safety program in your company? We’d love to hear your story!